Industrial Epoxy Flooring for Manufacturers: Pros & Cons
At Granite State Epoxy, we know how demanding manufacturing environments can be—especially here in Manchester, where over 200 manufacturers play a major role in the local economy. Your facility needs a floor that can take a beating from heavy equipment, foot traffic, and chemical exposure without failing. That’s why so many manufacturers turn to industrial epoxy. It’s built to handle tough conditions and offers impressive longevity. Still, like any upgrade, it’s worth weighing the pros and cons to decide whether epoxy is the right solution for your operation.
In this blog, we’ll explore the
pros and cons of
industrial epoxy flooring for manufacturers, helping you make an informed decision that’s best for your facility.
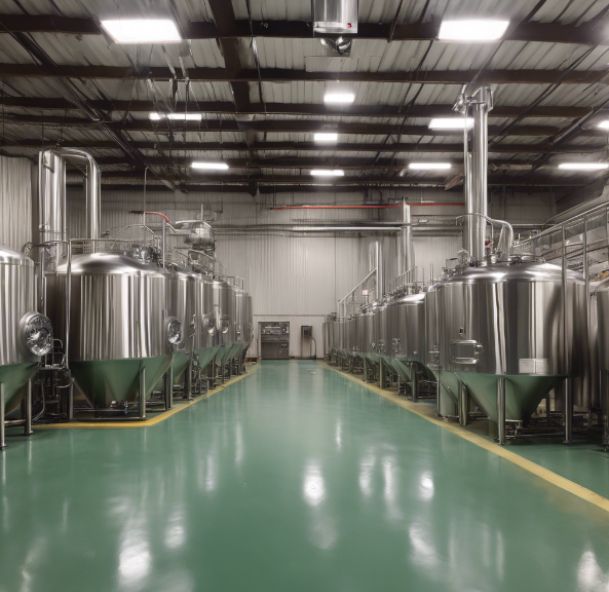
Understanding the Pros and Cons of Industrial Epoxy Flooring for Manufacturers
What is Industrial Epoxy Flooring?
Industrial epoxy flooring is a tough, protective surface created by mixing resin and hardener, which chemically bond and cure into a smooth, solid layer over concrete. It’s built to handle the demands of high-traffic environments like factories, warehouses, and production floors. Not only does it shield the concrete underneath from damage, but it can also be customized for specific industry needs—from added slip resistance to chemical protection.
The Pros of Industrial Epoxy Flooring for Manufacturers
1. Exceptional Durability
The durability of epoxy flooring is one of its greatest benefits in industrial settings. Epoxy coatings form a tough, seamless surface that can handle constant heavy traffic from forklifts, machinery, and foot traffic without cracking or deteriorating. With Manchester’s manufacturing industry employing approximately 8,941 individuals, facilities require flooring that withstands high foot traffic and the movement of heavy equipment daily. The hard resin provides a protective layer over the concrete, increasing its lifespan and reducing the need for frequent repairs.
- Withstands Heavy Loads: Whether you're moving large equipment or stacking products, epoxy floors resist damage from high weights and impacts.
- Scratch and Abrasion Resistant: Epoxy flooring holds up well against scratches and surface wear, unlike bare concrete, which can chip and deteriorate over time. This added durability helps your floors stay in better shape longer—both in appearance and performance—even in high-traffic or heavy-use areas.
2. Chemical Resistance
Manufacturing floors often face exposure to harsh substances—whether it’s oils, solvents, acids, or cleaning agents. Standard flooring materials can break down quickly under those conditions, but epoxy holds strong. It creates a non-porous, protective layer that blocks spills from seeping into the concrete below. For industries like automotive, chemical processing, or pharmaceuticals, that kind of resistance isn’t just helpful—it’s essential.
- Prevents Stains: Epoxy floors resist staining from chemicals, making them easier to clean and maintain over time.
- Reduces Damage Risk: Industrial epoxy floors protect your facility from corrosion or damage caused by chemical exposure.
As Manchester’s manufacturing sector has grown by 2.6% over the past five years, more facilities are adopting high-performance flooring solutions that provide long-term resistance to wear, chemicals, and spills.
3. Ease of Maintenance
Maintenance in a manufacturing facility can be time-consuming and costly, but epoxy flooring simplifies this process. Its seamless and non-porous surface makes cleaning and maintaining your floors easier and more efficient. There are no cracks or grout lines to trap dirt and debris, which can help reduce the time and effort needed to maintain a clean and safe working environment.
- Simple Cleaning: Epoxy floors can be cleaned quickly with a mop or a power washer, making it ideal for busy industrial spaces.
- Resistant to Bacteria and Mold: Because epoxy creates a seamless, non-porous surface, there’s nowhere for moisture, dirt, or bacteria to hide. That means less risk of mold growth and a cleaner, more sanitary environment—especially important in industries where hygiene matters.
4. Improved Safety
In any manufacturing environment, safety is a top priority. Epoxy flooring can help reduce accidents by adding traction where it’s needed most. With optional anti-slip additives, the surface can be tailored to handle wet, oily, or high-traffic areas—giving your team a more secure footing and helping you create a safer workspace overall.
- Slip-Resistant Finishes: Epoxy floors can be customized with textured additives that improve grip underfoot, helping prevent slips and falls. This added traction is especially helpful in areas where spills or moisture are common, or where forklifts and heavy equipment are in use.
- Enhanced Visibility: Epoxy flooring can brighten up your workspace by reflecting light, especially when installed in lighter or high-gloss finishes. This added visibility helps reduce dark spots and makes it easier to see what’s happening on the floor—whether you’re operating machinery, walking the line, or spotting potential hazards. Better lighting means a safer, more efficient environment for everyone.
5. Customizable Aesthetic
Epoxy isn’t just built to last—it also lets you tailor the appearance of your space to match your style or branding needs. You can choose from a variety of colors, textures, and finishes to match your company’s branding or improve how different areas are used. It’s a practical way to combine performance with visual appeal.
- Branded Flooring: Add your company’s logo, color scheme, or floor markings to guide traffic and define work zones. It’s a great way to improve organization and reinforce safety protocols at the same time.
- Clean, Professional Appearance: A polished epoxy floor gives your facility a clean, sharp look that speaks to your standards. It’s easy to maintain and helps create a first impression that shows you take pride in your operation.
6. A Cost-Effective Flooring Solution
Epoxy flooring might cost more at the start, but it saves money in the long haul. It holds up well under constant use, needs very little maintenance, and rarely requires repairs. That means less downtime and fewer unexpected expenses. In an industrial city like Manchester, where manufacturers rely on durable, low-maintenance solutions, epoxy flooring has become a smart, long-term investment that helps protect both the facility and the bottom line.
- Low Lifetime Costs: Its strength and resistance to wear help you avoid frequent repairs or premature replacement—saving money in the long run.
- Increased ROI: By protecting the concrete underneath and cutting down on repair costs, epoxy flooring helps manufacturers get more out of their investment. It’s a practical upgrade that adds real value over time—especially in facilities that run around the clock.
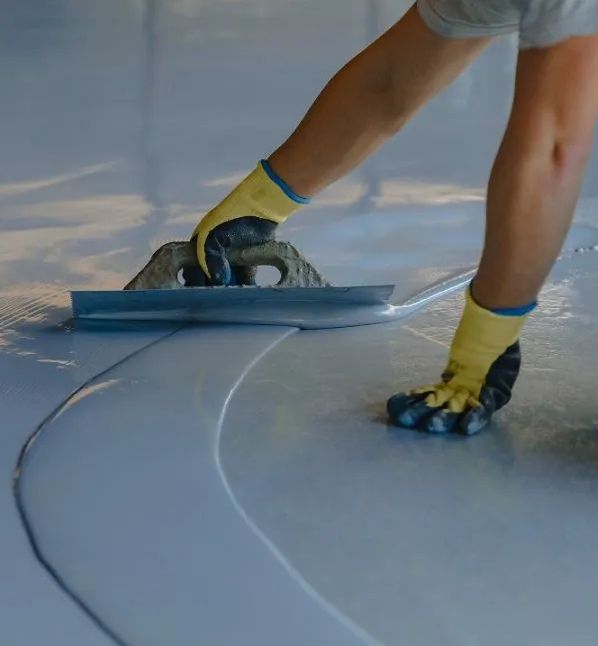
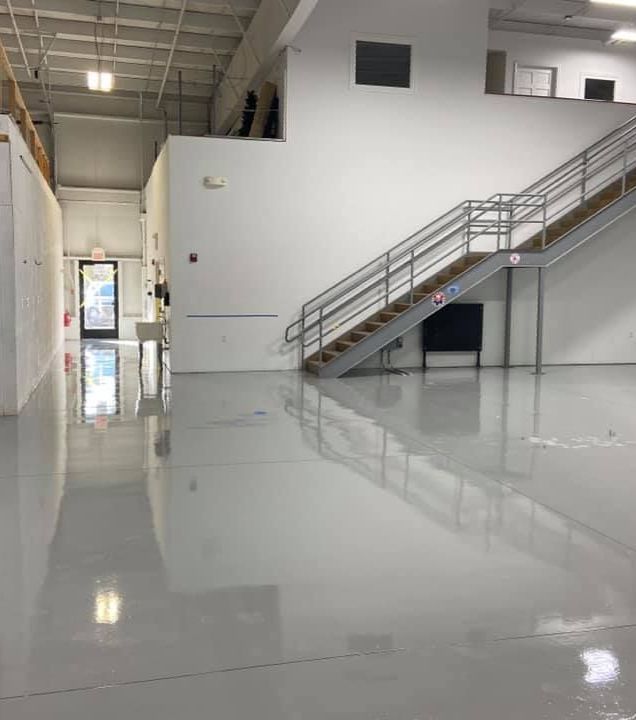
The Cons of Industrial Epoxy Flooring for Manufacturers
1. Long Curing Time
While epoxy floors provide incredible durability, one of the disadvantages is the time it takes for the material to cure. After installation, the epoxy coating needs to be left undisturbed for several days to fully harden and achieve its maximum strength. For manufacturers with tight schedules, this downtime can cause interruptions in operations.
- Extended Downtime: Depending on the size of the installation area, it could take several days to a week before the floor is ready for heavy use.
- Temperature Sensitivity: Epoxy coatings are sensitive to temperature and humidity, which can extend the curing time under certain environmental conditions.
2. Moisture Sensitivity
Epoxy flooring is best suited for dry conditions. If there’s excess moisture in the concrete substrate, it can lead to adhesion problems, resulting in bubbles, peeling, or an uneven surface. Moisture problems must be addressed before installation, adding time and potential cost to the project.
- Pre-installation Testing: Moisture levels in the concrete must be tested and mitigated before applying epoxy to ensure a successful bond.
- Risk of Delamination: If moisture is trapped beneath the epoxy, it can cause the coating to separate from the concrete over time.
3. Initial Cost
While epoxy flooring proves economical in the long run, the initial cost of installation can exceed that of other flooring solutions such as vinyl or tile. The materials, surface preparation, and professional installation contribute to the upfront expense. However, for most manufacturers, the longevity and durability of epoxy flooring offset the initial investment.
- Higher Upfront Investment: Epoxy flooring may come with a higher price tag for materials and installation compared to other types of flooring.
- Budget Considerations: When weighing flooring options, it’s important to look beyond the upfront cost. Epoxy may require more investment at the start, but the long-term savings in maintenance and durability often make it the more economical choice for busy manufacturing facilities.
4. Repair Challenges
Epoxy floors are tough, but they’re not invincible. Over time, heavy use can still lead to chips, cracks, or surface damage. Fixing those issues isn’t always simple—repairs usually need a professional, and getting an exact color or texture match can be tricky. That means even a well-repaired section might stand out.
- Professional Repair Required: Because epoxy isn’t easy to patch, most repairs call for experienced installers with the right tools and materials.
- Aesthetic Discrepancies: It can be hard to blend repairs perfectly, especially after years of use, which may leave visible differences in certain spots.
Is Industrial Epoxy Flooring Right for Your Manufacturing Facility?
Epoxy flooring brings real advantages to industrial spaces—it's strong, easy to clean, and adds a layer of safety that matters on busy production floors. But like any investment, it’s not one-size-fits-all. Your facility’s layout, workload, and environment all play a role in determining if epoxy is the best fit.
As Manchester’s manufacturing scene continues to expand, more businesses are turning to epoxy for its long-term reliability and lower upkeep costs. While it does come with a few challenges—like curing time and sensitivity to moisture—the long-term gains in performance, durability, and savings often make it a smart move.
\
Frequently Asked Questions
How long does industrial epoxy flooring last?
Industrial epoxy flooring is highly durable and can last anywhere from 10 to 20 years, depending on the environment, foot traffic, and proper maintenance. In high-traffic manufacturing areas, routine care and cleaning will help extend the lifespan of the floor.
Can epoxy flooring handle heavy machinery and equipment?
Yes, industrial epoxy floors are designed to withstand the weight of heavy machinery, forklifts, and other equipment without cracking or becoming damaged. Epoxy’s compressive strength makes it ideal for manufacturing environments with frequent equipment movement.
Is epoxy flooring safe for manufacturing environments with chemical spills?
With its high resistance to acids, oils, and solvents, epoxy flooring is an excellent option for manufacturing facilities. Its ability to withstand chemical spills ensures your floors remain unblemished and long-lasting.
How long does it take to install epoxy flooring in a large facility?
The installation time for epoxy flooring depends on the size of the facility and the condition of the concrete substrate. Typically, installation takes anywhere from 2 to 5 days, including curing time. Large facilities or areas requiring extensive surface preparation may take longer, but our team at Granite State Epoxy works efficiently to minimize downtime.
Contact Granite State Epoxy for Expert Epoxy Flooring Solutions
At Granite State Epoxy, we provide professional epoxy flooring installations designed to meet the demands of industrial and manufacturing environments. We can assist you in determining if epoxy flooring is the best choice for your facility, and we’ll guide you from the initial surface prep through the complete installation process.
Call us today at
603-232-0117 to schedule a free consultation, or
fill out our online
form to get started on your industrial epoxy flooring project. Let Granite State Epoxy deliver a durable, cost-effective flooring solution that enhances manufacturing operations.